Denounce with righteous indignation and dislike men who are beguiled and demoralized by the charms pleasure moment so blinded desire that they cannot foresee the pain and trouble.
Read MoreOur team has developed an entirely different approach which addresses almost all the challenges encountered by use of conventional means of effluent water / fluid treatment.
Rather than deploying a complex in-series multi-staged process that treats the effluent in various phases, our developed process system oxidizes a broad spectrum of pollutants within a singular process called Hydro-Oxidation (HO).
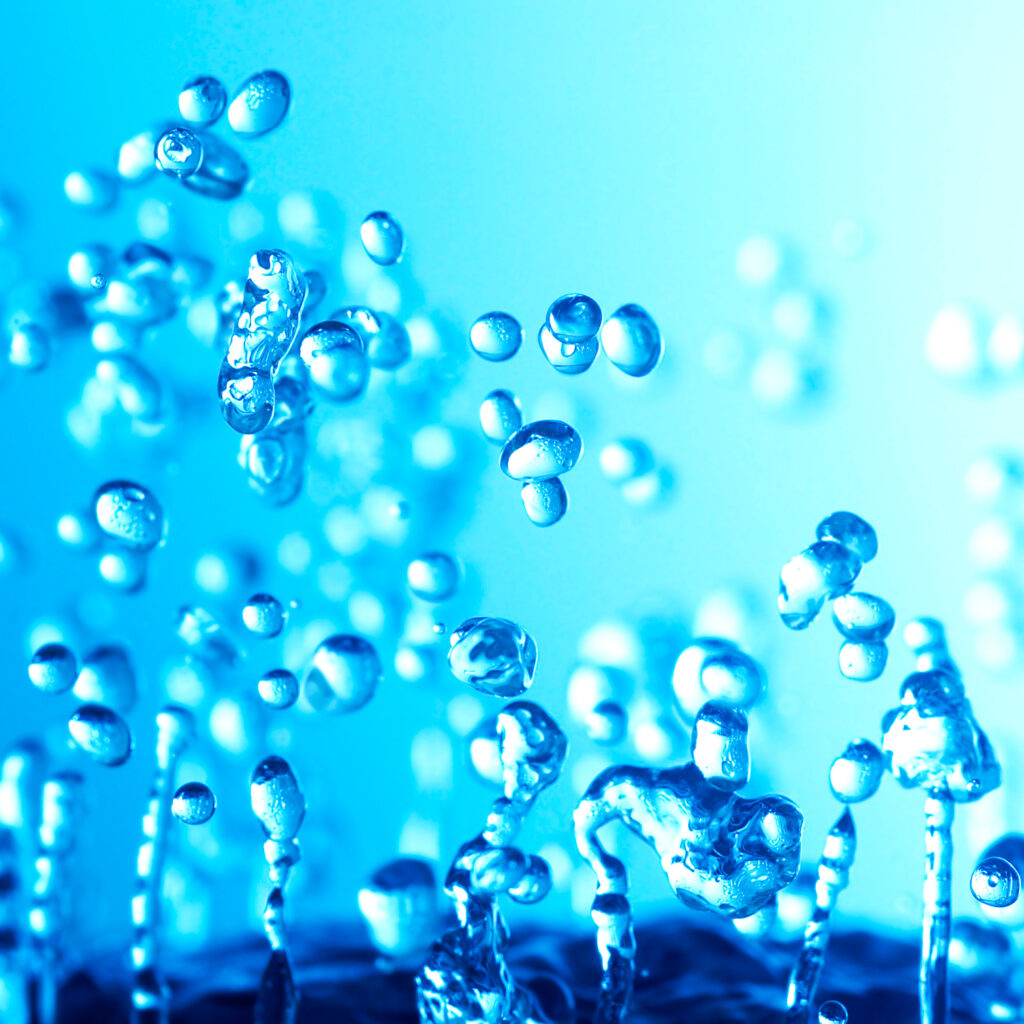
Our process technology involves treating the fluids through Hydro-Oxidation (HO) using its own especially in-house empirically developed metallic based ‘enabler’ catalysts, which release high potential molecular oxygen forcefully fed to the compounds within effluent fluid.
To achieve these simultaneous reactions, we have integrated our enablers within the HO process unit which create collisional forces (measured in angstroms) in the fluids to be treated. To support these collisional forces, certain radical accelerant solutions are also dosed into the process which are routed through our specially designed and controlled electrodes
Futura HO Process = Effluent fluid + Enabler Catalyst + DC Current +/- Accelerants
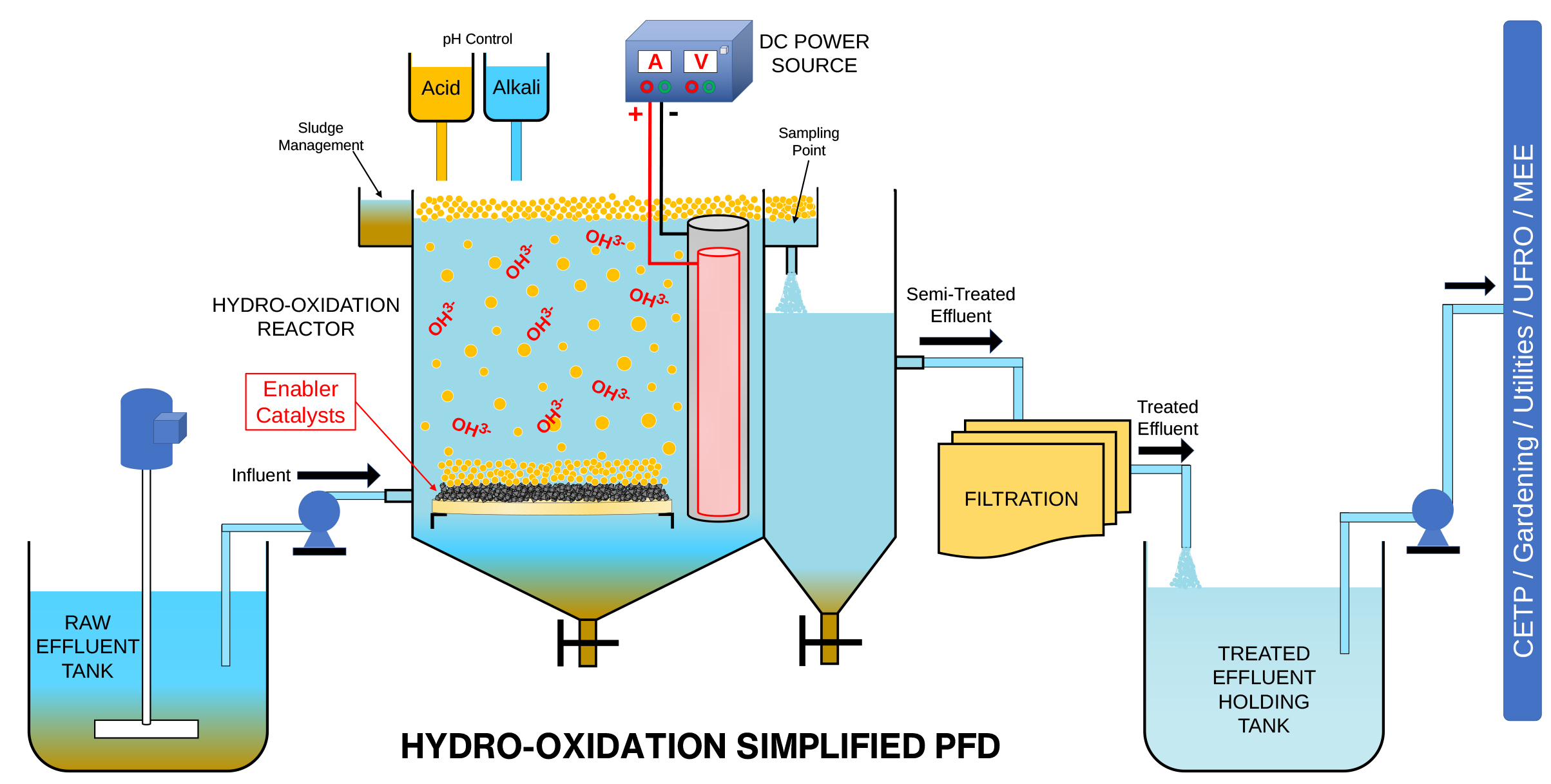
With the assistance of the reactions that take place therein, the pollutants (organic and inorganic) in the effluent / process fluid starts to disintegrate out of the fluid molecule and coagulate into heavier particles which collect (depending on the density of the pollutants) either at the bottom of the reactor tank or at top of the fluid as floating sludge solids which are skimmed off or filtered out. For many effluents, during HO reactions, the dissolved solids may get oxidized and come into suspension.
INLET to Futura HO Reactor = Effluent Fluids
REACTORS inside Futura HO System = Enabler +/- Accelerant + DC current
OUTLET from Futura HO Reactor = Pollutant Free Fluids + Sludge
- Bacteria / Coliforms / Cysts / Algae
- Total Suspended Solids (TSS) [Clay, Coal, Silt, Silica, Dust, etc]
- Heavy Metals Removal / Separation
- Fats / Oil / Grease
- Chemical Oxygen Demanding Impurities [COD]
- Ammonical Nitrogen [NH3-N]
- Phosphates Removal / Separation
- Biochemical Oxygen Demanding Impurities [BOD
- Total Dissolved Solids (TDS)
- Colloidal and Reactive Silica
- Upto 99%
- 95% +
- 95 % - 99 %
- 93% - 99%
- 95 % +
- 95 % +
- 80 % +
- 90 % +
- uptp 25 % +
- In certain Aliphatic Chemistries
- 93 % +
We approach every effluent case in a methodical and a scientific manner. Before submitting a price quote, we require the client to provide us with a sample of their effluent, which we then run through our laboratory to ensure we can treat it effectively. Moreover, for Greenfield projects, we emphasize that the client must supply a synthetically produced effluent sample that is representative of their R&D.
Feasibility Study
A questionnaire is first received where we review the effluent characteristics, compounds present, problems statement and the purpose very well with subsequent calls
Step 01
Treatability Study
Once we are convinced, only after we will request for effluent representative samples to be sent to our lab. Your effluent is subjected to multiple treatability studies and protocols to practically evaluate the best possible outcome and most optimized treatment protocol. A detailed report is tables with complete basic design- PFD, Water Balance, Lab Test Results with budgetary CAPEX and OPEX numbers.
Step 02
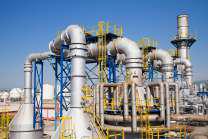

Pilot Plant Study
In cases where the client wants to gain further confidence, we also offer on premise pilot trials for your effluent runs. Our pilot plants range from 1 KLD to 5 KLD capacity.
Step 03
Commercial Quote
Finally a price quote is submitted after completing the treatability studies on your representative sample of effluent, along with PFD/Schematic, Water Balance, best possible commercially viable scheme, with firm CAPEX, OPEX, plant footprint with overall dimensions of key equipment. Page